Common Mistakes When Checking For Leaks
Vital Know How, If You Gas Flush Your Products
During a recent site visit to a meat factory, we noticed that, despite having multiple packing lines, they only intermittently tested for leaks during their 24/7 production, using a single bubble tank.
Firstly, lets address the elephant in the room. Bubble tanks are okay and serve a purpose, but only if you have:
- a low budget
- need to check for leaks on non-gas flushed products
- have operators who can spot the smallest of bubbles.
We also sell them – please have a look at look at the Dansensor LeakPointer H20. However, on this occasion, the customer was gas flushing, across all of their lines and operators placed finished packs in the bubble tank, walked away and left them under vacuum for several minutes.
When they returned, they would check for significant pack deflation and rework if necessary, or wipe down and send the packs to the end-of-line packing. The results were recorded on paper.
We also have the Dansensor Lippke 5000, our latest, advanced, seal integrity instrument. This unit can include a test to inflate the internal pressure within the pack, which can then be placed in a water bath and checked for bubbles.
Both of these instruments can be used to check non-MAP packs.
So, what are the issues with this particular customer using their bubble tank?
Subjectivity:
- Operators make subjective decisions about whether a pack has leaked
- Even though the pack was left in the tank for a number of minutes, it means that micro leaks would not be detected, as they take some time to show under water.
Hygiene:
- Under vacuum, micro leaks will very slowly suck water into the packs. If no leak is detected with the eye, water enters the bag and is a possible catalyst for product spoilage and unwell customers!
Waste:
- Film is wasted because packs need to be opened and film binned, as is the product.
Data Integrity:
- Results recorded manually can lead to data loss, or errors.
A Much More Effective Way to Test For Leaks
Dansensor LeakPointer 3
The Dansensor LeakPointer 3 creates a pressure difference between the pack and the chamber, which is preset and specific to each pack size. If there is a leak, the pressure difference causes the CO2 inside the pack to leak into the chamber and the device detects this CO2 trace.
Leaks through perforations as small as 50-micron can be detected.
The display shows a pass, or fail image once the test is complete, providing a clear, objective indication of whether there is a leak.
Advantages of the LeakPointer 3:
- Objective Testing – the decision is made by the instrument, not the operator
- Quick Results – testing time ranges from 10 to 35 seconds
- Non-destructive – if no leak is detected, packs can be sent through to end-of-line packing without damage
- Paperless QA – all test results are stored electronically and can be exported as a CSV file via USB, or LAN connection.
How We Were Able To Help and Reduce Their Customer Complaints By 95%
The customer agreed to used the Dansensor LeakPointer 3 for a two-week loan period and the results were more than impressive. Many more leaks were detected and which the traditional bubble tank method would have missed. This lead to a 95% reduction in customer complaints about leaking packs.
Contact Our Sales Team
01223 492083
sales@tendringpacific.com
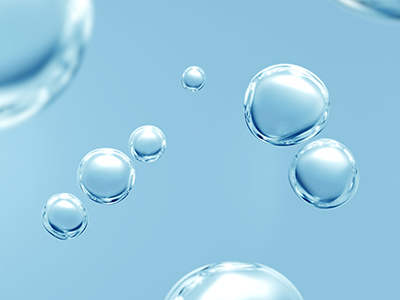
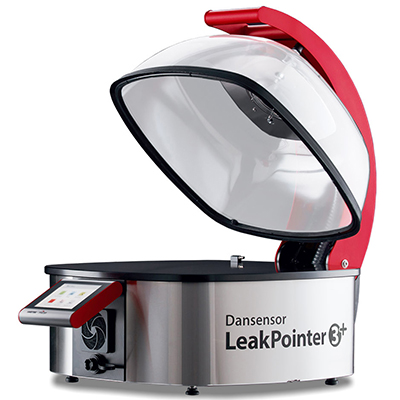
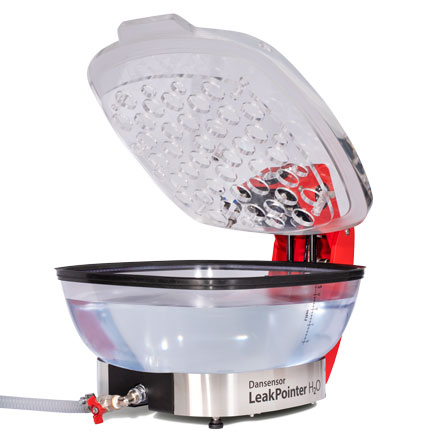
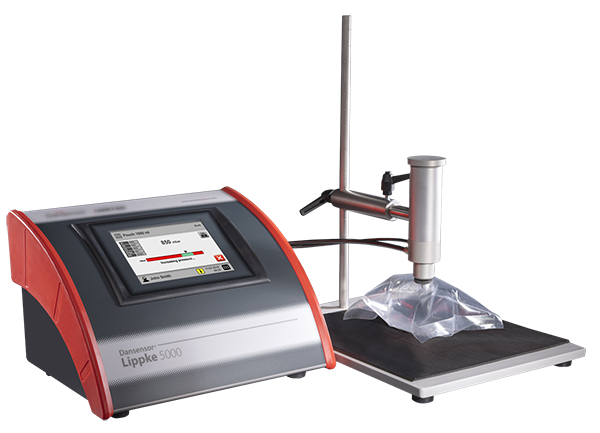
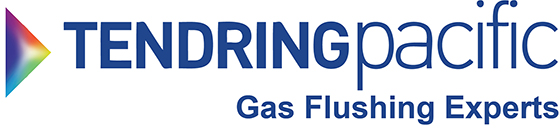