Leak Testing – Destructive and Non Destructive Options
A Practical Review of Destructive and Non Destructive Leak Testing
Leaking MAP packages are a major concern for all food packers. They trigger several consequences and most of them land back with the packaging company:
- safe product delivered to the customer
- product with reduced shelf life
- increased food waste
- increased packaging waste
- significant financial penalties per pack return
- damage to brand and customer reputation
- damage to packer reputation
- loss of contracts
Even a hole as small as 50 micron will cause the pack headspace to revert to atmosphere within 3 days. Of course, such small holes can be difficult to detect, but not impossible. We have several excellent solutions from the Dansensor range to help you cut your leaker rate to an all time low.
For example, putting a non destructive Dansensor LeakMatic II at the end of the production line has helped one of our customers bring their leak rate down from 17% to just over 2%. A dramatic reduction with significant financial and reputations benefits.
Leak Detection Methods
Hand Squeeze The Pack in a Bowl of Water
This is a very popular test method and works when the holes are large and the leaks obvious. The bag is simply held under water by hand and squeezed as hard as possible. A stream of bubbles reveals the position of any hole.
Disadvantage
In many instances this method will not identify leaks from small holes. These only show when the packaging is placed under a much higher pressure than can be generated by hand – and particularly hands that are cold and tired by frequent testing. Very small holes are more easily identified using the vacuum water test chamber.
Destructive/non destructive?
Bags that show no bubbles in the water bowl test are often wiped down and sent out. The test would be regarded as non-destructive. However, if there is an undetected micro leak, water will ingress into the hole and there is a high probability that bath water will contaminate the pack, turning it, in effect, into a destructive test.
Vacuum Water Test Chamber
The test pack is immersed in the vacuum tank, the lid closed and a vacuum applied. As a result, the pack inflates from the gas inside and the differential pressure forces gas out through holes and/or sealing faults.
Advantage
Even very small holes can be detected. The stream of bubbles identifies the exact position of the fault and when present in several packs, it helps to determine which sealing jaw is underperforming. Being able to direct an engineer to the exact location of the problem, helps reduce line down time.
Destructive/non destructive?
If no bubbles show, then the pack can be regarded as having no leaks, can be confidently wiped down and sent out. A non-destructive test. Where packs show leaks, the test is destructive and they must be discarded. There is no way of measuring, and therefore knowing, how rigorous a test is being performed.
Dansensor Leak Testers
LeakPointer 3 and LeakPointer 3+
Reliable non-destructive offline manual testing of single packs. Reliably capable of detecting leaks, as small as 50 microns (µm). A vacuum operation with the detection of trace gas CO2. A repeatable differential pressure between the inside of the pack and the test chamber, can be created and easily verified. This gives a consistent rigor to the test being preformed. The LeakPointer 3 is designed for single pack testing and the LeakPointer 3+ for multiple pack testing.
LeakMatic II
Fully automated, end of line, non-destructive leak detection system for crates and cartons. Extremely sensitive using CO2 as a trace gas. Microleak detection.
Lippke 5000
A destructive test for quantifiably determining the strength of a pack seal. Ideal for ensuring that the sealing parameters of the jaws and die sets are selected and performing optimally, particularly when changing film materials, or starting to use new packaging materials.
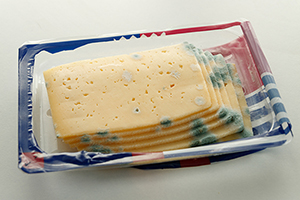
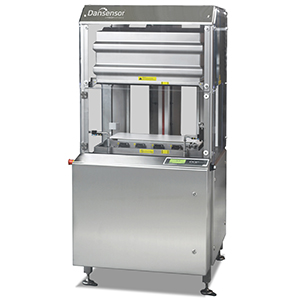
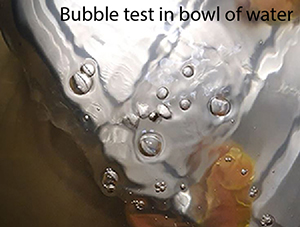
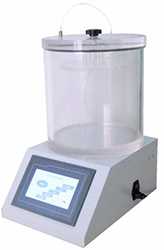
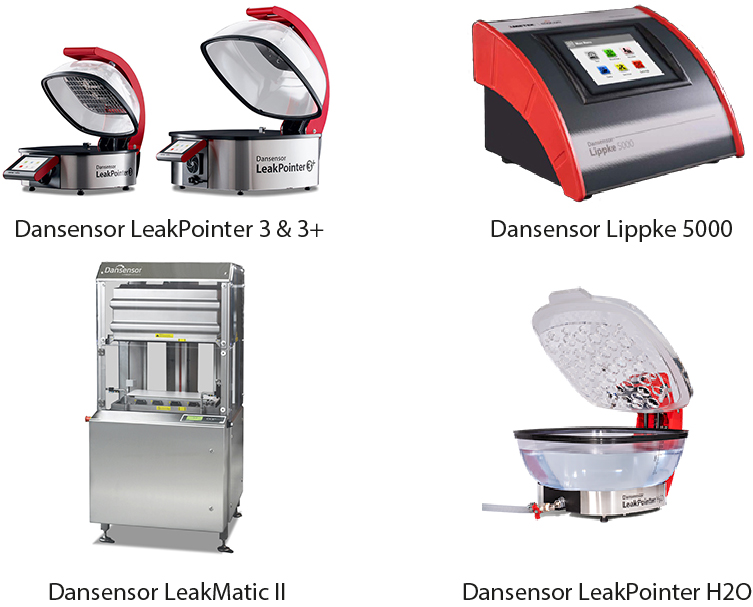