Optimising The Gas Flushing Process
The immediacy and relentlessness of production deadlines mean that most production facilities have to live with a range of ongoing problems.
Solving them on the go with ‘quick fixes’, the only way to get things done to timescale. But left unattended, they can and develop into something much more serious and damaging to both efficiency and reputation.
Partnership with Tendring pacific
We sell effective solutions, that help solve production line problems, make processing plants more effective, reduce waste, save costs and make lines more efficient.
It might be that when you tell us the problem, we’ll know the solution stright away. We’ve been working in the industry for over 15 years and gained some incredible insight from thousands of conversations with engineers and production managers. It’s made us a very credible and effective team. When that’s combined with the reliability of Dansensor gas flushing equipment, it puts us at the leading edge.
Optimising The Gas Flushing Process
Typical and regular problems that we hear from customers include:
Not getting enough gas in the pack, resulting in poor product appeal. Inconsistency in label positioning, orientation and pack deflation just some of the consequences. For consistency and control of gas flow we’ve the MAP Mix Provectus, buffer tank options and the MAP Check 3 Pressure.
The flow of flushing gas not being in sync with the changing speed of the packaging machine. This often results in variable residual oxygen remaining in the pack, which presents an otherwise inexplicable series of intermittent mold, or off complaints. This is a growing area where our Smart Factory, real time data streaming is drawing a lot of attention.
The rate of production has slowed through gas starvation, caused by inadequate replenishment of the buffer tank by the start of the next cycle.
Understanding how much gas has been used on the latest production run compared with previous ones. Monitoring readings from our online equipment can hightlight excessive use of gas. Monitoring trends in the data can highlight potential breakdowns that early maintenance can prevent and timed to minimise production downtime.
The sealing of packs is incomplete, creating leaks and causing an increase in mold or off complaints. The offline Dansensor LeakPointer 3 and 3+ will detect leaks from holes as small as 50 microns. We’ve an online leak detector as well in the LeakMatic II
Scheduled maintenance being carried out too late to prevent an increase in machine stoppages & production of sub-standard product. Our Preventative Maintenance Guides are a helpful reminder of what needs to be checked and how to fo that most efficiently.
High levels of destructive quality control testing is causing the quantity of product & packaging waste to be too high. Being better able to contol the gas flow and gas mix earlier in the process can significantly reduce the volume of testing later in the line. Our MAP Gas Flow Checks have helped many customers tackle this issue.
If you’d like to have a chat about the things you’re looking to improve and share the problems with us, we’re hear to both listen and partner the solutions with you. Call 01223 492083 or email sales@tendringpacific.com
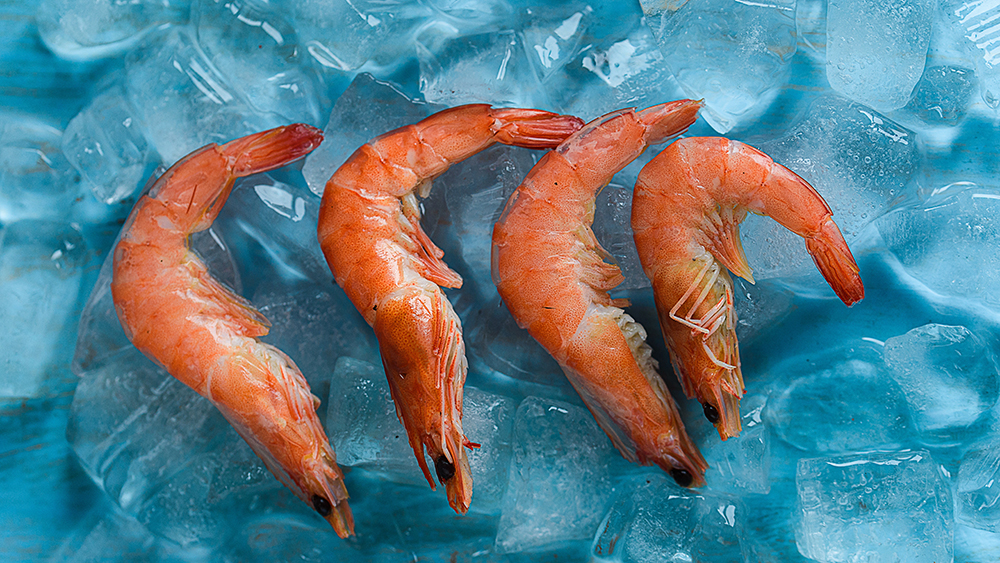
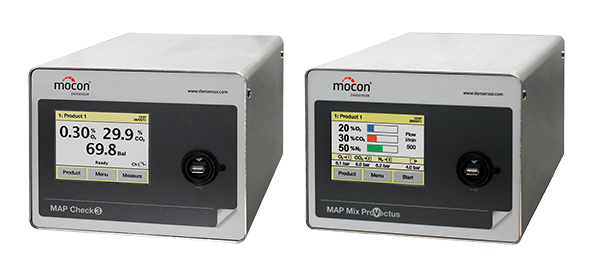
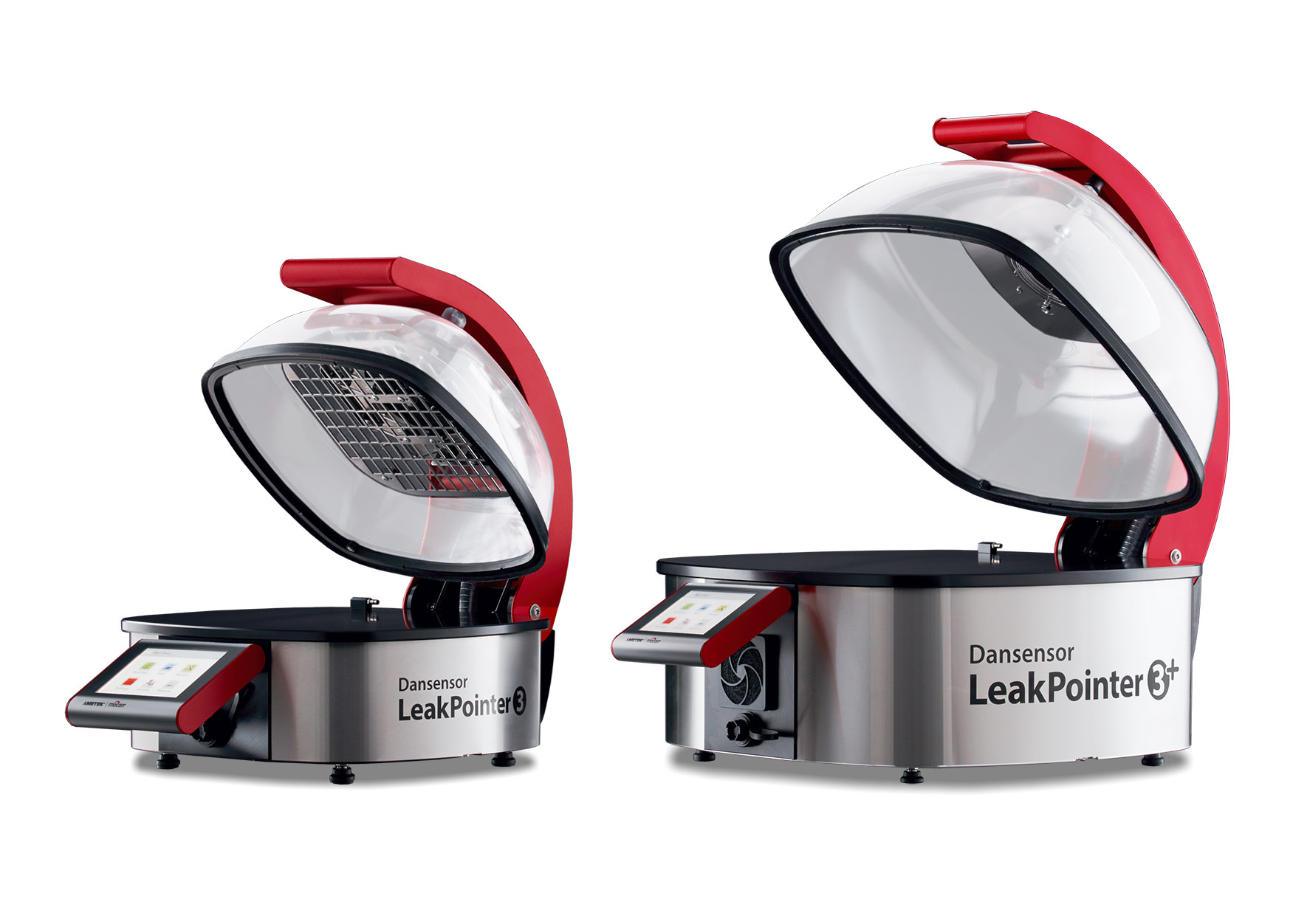
Contact Our Sales Team
01223 492083
sales@tendringpacific.com