
Dansensor MAP Check 3 Vacuum Online Headspace Gas Analyser
Monitoring Headspace Gas at the End of the Packing Cycle on Tray Sealing and Thermoforming Lines
Monitors the %O2, or the %O2 & %CO2, from the packs at the end of the each cycle of the packaging machine, checking 100% of production, in realtime.
The MAP Check 3 Vac produces highly accurate results, with excellent correlation to the average of the destructive offline tests. It reduces the time spent on offline quality assurance checking and eliminates the packaging waste created by carrying out those checks.
The test data can be automatically downloaded to Paperless QA software – consigning offline checks to a verification role. The MAP Check 3 VAC can be installed onto new lines, or retro-fitted onto existing one.
Process A gas sampling point is mounted in the die of the packaging machine, from which a gas sample is taken each and every cycle. At the very end of each gassing cycle, the mix percentages of that gas sample are the same as the average of all the packs being sealed in the die.
The MAP Check 3 VAC calculates the percentage balance and compares the %O2 and %CO2 with the target levels set by the user for that specific product. If either the %O2 or %CO2 results are outside of permitted limits, the unit will automatically stop the packaging machine from producing further cycles containing an incorrect mix, until the issue has been resolved by the operator.
Automatic Data Download The results can be automatically downloaded via a LAN or RS232 port to Paperless QA software for subsequent review & recall. This eliminates the need for creating hard copy records, with their inherent transcription errors and need for bulky storage. Trending the thousands of test results produced each week and month can often reveal the gradual decline in packaging machine performance over time. Preventative maintenance can then be scheduled according to need, rather than simply by time interval and so improving the overall equipment effectiveness (OEE) & operational profitability.
Correct Gas Mix The MAP Check 3 VAC can be connected electronically to the Dansensor MAP Mix Provectus gas mixer. Selecting the required product set up on the MAP Check3 VAC will automatically select the correct gas mix for that product. The Paperless QA software will also automatically record the mix selected and the volume of gas consumed in the production of the run.
Buffer Tank Sampling The volume of plastic packaging waste from a production line can be reduced further by adding the “Buffer Tank measurement” option to an installation. Via the MAP Check 3 VAC touch screen, the user can take a gas sample from the packaging machine’s buffer tank for analysis. This avoids the common practice of running a few cycles of empty packs to test the buffer tank gas and significantly reduces the number of empty packs going to landfill.
Waste Reduction Environmental concerns and reduction of packaging waste are high on the agenda of the food industry. By using the online non-destructive testing of the MAP Check 3 VAC, packaging waste can be reduced. For example, from each production line testing 6 packs every 30 minutes on a double day shift and a 5 day working week, 6 packs x 2 x 16 hours per 350 days per year = 67,200 packs to landfill each year plus wasted product.
Oxygen measurement (zirconia sensor) | Standard in all models |
---|---|
Carbon dioxide measurement (dual beam infrared) | Model dependent |
Control of MAP Mix Provectus | Yes |
Number of test programs (devices with LCD display) | Up to 1000 |
Measuring range | 0-100%, both O2 and CO2 |
Resolution | O2: ≥10%, 0.1; <10%, 0.01; <1%, 0.001 CO2: 0-100%, 0.1 |
Sensor accuracy O2 and CO2. System accuracy depends on die geometry and machine timing | O2: ≥0.1%, ±1% of reading; <0.1%, ±0.001% absolute CO2: 0-100%, ±1.5% of reading + 0.5% absolute |
Heating time | 10 min |
Models | Available with LCD display or as “Black Box” without display |
---|---|
Connections | 2 x RS232C, LAN 10/100 Mbit (Modbus TCP), USB, host for import/export, 24 VDC logic for machine control signals and alarms |
Dimensions & weight | 192 x 230 x 375 mm (H x W x D), 8.5 – 11.5 kg (depending on model) |
Power supply | 103-132 / 207-264 VAC (auto ranging), 47-63 Hz |
Compliances | CE |
Further Benefits and Options
To streamline installation, Tendring pacific offers:
- Fittings Kits – 2 versions N2/CO2 only and O2
- On-site installation and training by our installation engineers
- IP 54 Stainless Steel Enclosure for use in both wet and dusty environments
- Warranty Upgrade
- Annual Service Contracts and Preventative Maintenance Contracts
- Plantstats QC Pro, paperless QA software for data collection with email/SMS alerts
- Buffer Tanks installed for complete central mixing capability
- Dansensor MAP Mix Provectus – for total control.
Contact Our Sales Team
01223 492083
sales@tendringpacific.com
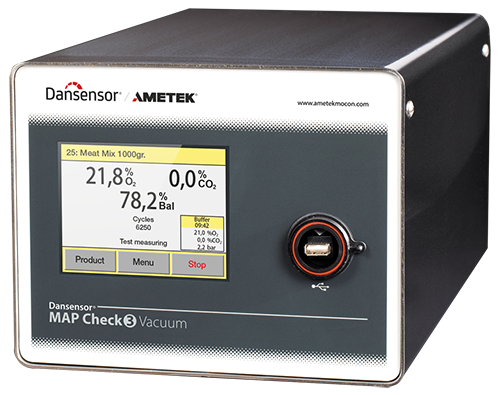
Dansensor MAP Check 3 Vacuum Preventative Maintenance Guide
How To Videos for the Dansensor MAP Check 3 Vacuum
Click Here »Book a Demonstration
Contact our sales team
01223 492083
sales@tendringpacific.com
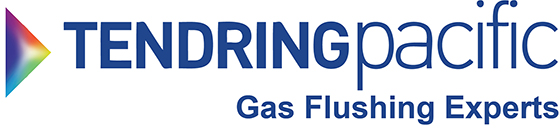